-
About UsMTL has been focusing on investment casting, including not only carbon steel metal components, but also stainless steel products and alloy steel products.
-
-
FactoryMTL has been focusing on investment casting, including not only carbon steel metal components, but also stainless steel products and alloy steel products.
-
NewsMTL has been focusing on investment casting, including not only carbon steel metal components, but also stainless steel products and alloy steel products.
Investment Casting Core Principles
Apr 16,2025
The shape of the part is reproduced by wax mold, and the wax is melted away after the refractory shell is formed by utilizing the solubility of wax (melting point is about 50-70℃), forming a complete cavity without parting surface, avoiding the problem of mold dislocation in traditional sand casting. Key steps:
The shape of the part is reproduced by wax mold, and the wax is melted away after the refractory shell is formed by utilizing the solubility of wax (melting point is about 50-70℃), forming a complete cavity without parting surface, avoiding the problem of mold dislocation in traditional sand casting.
Key steps:
Wax mold making: Wax material (paraffin + stearic acid, etc.) is pressed by pressing mold (metal mold) to form a single or combined wax mold (module).
Shell coating and dewaxing: Quartz sand + binder (such as silica sol) is coated on the surface of the wax mold layer by layer, and a 5-10mm thick shell is formed after drying. The wax mold is melted away at high temperature (80-90℃) to obtain a hollow shell.
High temperature roasting and pouring: The shell is roasted at 900-1200℃ to remove impurities, and molten metal (such as stainless steel, high temperature alloy) is poured in. After cooling, the shell is broken to obtain the part.
PREVIOUS:
CONTACT US
Office Add:No. 51 Fuqian St., EDZ, Dongying, Shandong, 257091 China
Plant Add:No. 88 Lingzhihou St., EDZ, Gaomi, Shandong, 261500 China
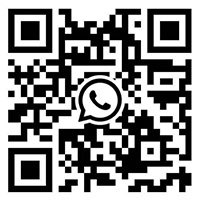
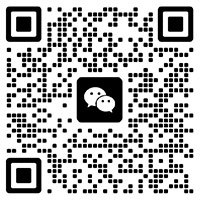
POPULAR PRODUCTS
CONSULTAR
Copyright : Dongying Maitlai Import and Export Co., Ltd. Powerby : CEGLOBAL | SEO | Privacy agreement